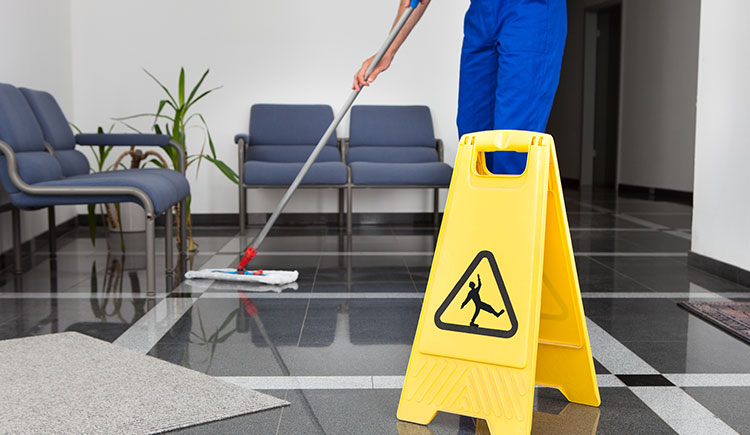
Performing Your Own Annual Workplace Safety Audit
A safe workplace should be a priority for every small business owner. Businesses must conduct regular safety inspections to identify hazards and then take the necessary corrective measures to address them. OSHA can also potentially conduct unannounced inspections that can result in costly fines. Short of waiting for the results from government inspections, how can owners be sure their own safety programs and strategies continue to meet internal goals and standards? The answer – regular workplace safety audits.
Audit vs. inspection
Workplace safety audits and workplace safety inspections are not the same thing, though both aim to keep workplaces safe and both use safety checklists. Audits do not replace regular safety inspections at the workplace. Audits examine workplace safety guides, programs, practices and training to ensure they are reliable, effective and meet the business’ safety goals and standards. Inspections search for the actual safety hazards, risks and poor practices in the workplace that could cause injuries or illness. Objective third parties or employees from other departments usually perform workplace safety audits, while people familiar with the workplace usually perform safety inspections.
OSHA requires small business owners provide safety training and submit to safety inspections, but it does not require owners to conduct safety audits. Audits can help make sure a business is in compliance with OSHA safety regulations and requirements. OSHA will not ask for safety audits before performing its inspections, but it may ask for audits as part of an ongoing review to ensure owners have corrected self-identified safety issues prior to an inspection or made efforts to prevent a safety issue from reoccurring.
However, OSHA does view workplace safety audits as part of a good safety plan. It offers a workplace safety audit guide to help small business owners understand the scope of a good audit. It includes checklists for management leadership; worker participation; hazard identification and assessment; hazard prevention and control; education and training; program evaluation and improvement; and communication and coordination for host employers, contractors and staffing agencies. This helps owners see whether their safety guidelines have been ignored, partially implemented, implemented with minor deficiencies or fully implemented.
Four main questions
Small business owners interested in implementing workplace safety audits should begin by creating an auditing team made up of several people from different departments within the business, leading safety website SafetyInfo advises. For objectivity and accuracy, members should not audit their own areas of the business or an outside qualified safety consultant should be hired.
SafetyInfo suggests a sound audit should provide comments, recommendations and corrections that answer four main questions:
- Does the program cover all regulatory and best industry practice requirements?
- Are the program requirements being met?
- Is there documented proof of compliance?
- Is employee training effective – can and do employees apply specific safe behaviors?
To answer those questions accurately and comprehensively, a workplace safety audit will have several phases:
- Preparation: Alert affected staff; compile safety documentation; review jurisdictional requirements; and map out the audit’s scope and schedule times for the audit.
- Fact-finding: Then, gather all relevant safety information and hand out proper background information and documents; audit leaders should assign team members to inspection areas; auditors investigate to see if documentation is correct, workspaces and workers observe safety practices, safety training happens consistently and company safety practices and programs meet jurisdictional requirements.
- Review and report: Next, the auditing team should review all findings and write a comprehensive report that answers the four main questions, as noted above. The report should note successes and failures in all audited areas. It should also include recommendations to correct the mistakes the audit reveals, followed by taking corrective actions in order of highest to lowest priority.
- Recommendations discussion: Finally, the workplace safety audit results should be published and distributed to departments, managers and supervisors to make them all aware of the basic findings and corrective actions needed and taken. Here, owners also have an opportunity to laud the good work staff members have done to promote and preserve safety in the workplace and inspire the staff to continued safety success.
OSHA notes when workers stay safe and healthy, small business owners’ direct costs-savings may include lower workers’ compensation insurance costs. Reduced indirect costs can include increased productivity and morale, better quality products, improved labor and management relations and improved employee retention.
EMPLOYERS® is committed to helping small businesses operate safer, more efficient workplaces. Contact EMPLOYERS® today to learn more about our cost-effective workers’ compensation insurance.
EMPLOYERS®, America’s small business insurance specialist® and EACCESS® are registered trademarks of EIG Services, Inc.
The information provided is intended to provide a general overview. This information is not legal advice and should not be relied on as such. EMPLOYERS® makes no warranties for the accuracy, adequacy, or completeness of the information provided, and will not be responsible for any actions taken based on the information contained herein. If you have legal questions or need legal advice, please consult an attorney.