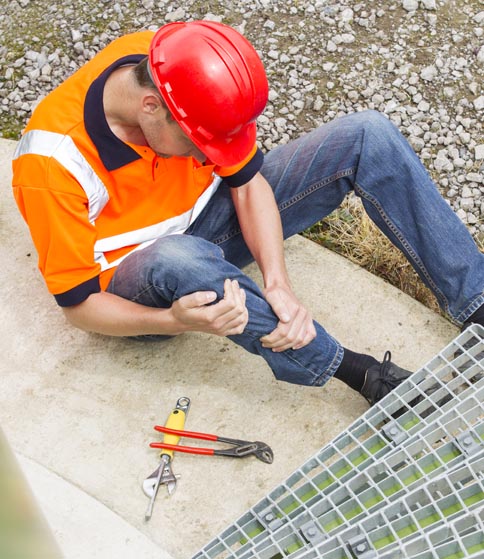
Workplace Safety for Property Managers
A property’s gutters need cleaning, the landscaping needs upkeep and light fixtures need changing. A property manager’s to-do list is never-ending – and that’s just for a single site! It’s impossible to be at all properties simultaneously to make sure the maintenance staff gets all those jobs done safely.
Out of sight too often means out of mind, and accidents can happen.
So how are property management employees really being injured? And how can you help prevent these injuries?
Property Management Common Injuries and Causes
According to the U.S. Bureau of Labor Statistics’ (BLS) most recent data, more than 1,700 property, real estate and community association managers sustained injuries while on the job in 2018. This included 700 incidents of soreness or pain; 260 fractures; 70 sprains, strains and tears; 30 cuts/lacerations; 20 multiple traumatic injuries; and 630 injuries of “another nature.”
In his line of work, EMPLOYERS Western Region Loss Control Manager Raul Chacon often sees a range of injuries in the property management sector.
Slips, Falls, and Ladders
“Slips and falls are two of the primary types of injuries that happen, mainly because, depending on the property, workers may be exposed to slippery or wet surfaces,” he says. “Whether it’s removing snow from the parking lots or entryways, or even just cleaning floors, there are inherent risks for injury at the ground level.”
Injuries above ground, particularly involving ladders, are also common for property managers.
“It could be that they’re either doing some touch-up painting, removing leaves from roofs, gutter repair, doing some caulking around some windows – the types of things where they’re planting ladders on uneven grounds and not using good precautions, good safety procedures or best practices when using a ladder,” Chacon says. “Those situations are more unique to property management and often the causes of slips and falls.”
[An overconfident worker will] think, ’I can drive a car, so I can certainly drive a forklift or a power lift.
Power Equipment
In the course of property maintenance, workers often use a variety of light and heavy equipment and machinery. When not used properly, workers risk lacerations, fractures, burns or worse.
“Power washers, for example, where they may be preparing to do some touch-up painting or maybe some repairs on walls, can cause injuries,” Chacon notes. “Many times, workers don’t use good personal protective equipment, such as goggles or a face shield, so the back splash gets in their face. Then there’s the stuff that they’re moving off the wall or off the surface that they’re trying to clean, which could contain hazardous materials, such as asbestos.”
Another common mistake is when a worker tries to operate equipment or machinery with little or no training. “Property managers will sometimes have a worker who thinks it can’t be that hard,” Chacon says. “They think, ‘I can drive a car, so I can certainly drive a forklift or a power lift.’”
Common Injuries These are among the most common injuries in property management:
Injury | Description | Causes | Prevention |
Fractures | Bone breaks due to trauma or overuse | Most common in jobs involving manual labor and exposure to heavy equipment and machinery | Proper training and ergonomics can help prevent these sorts of injuries. In an environment where moving heavy equipment is common, increased supervision or spotting by other workers is another preventative measure. |
Sprains and strains | Sprains are stretched or torn ligaments, while strains are stretched or torn muscles and tendons. | Any type of falling, twisting and pulling can cause sprain or strain injuries. In the workplace, improper lifting or ergonomics are often the causes of these types of injuries. | Familiarize yourself and your employees with the U.S. Occupational Safety & Health Administration (OSHA) lifting guidelines and ergonomics guidelines. |
Lacerations | Deep cuts or tears in skin or flesh | Often when workers rush to finish a job, lose concentration or don’t wear the proper safety gear, such as cut-proof gloves. | Help educate employees on wearing the most appropriate safety gear for the job they are doing. |
Contusions | Bruises or contusions are marks on the skin that occur when small blood vessels are crushed and blood becomes trapped under the surface, but the skin does not open | In the workplace, this type of injury usually happens when employees drop objects due to improper lifting or when they bump into things. | Regularly train and review proper ergonomics and environmental awareness, which can usually prevent these sorts of injuries. |
Slips/Trips | Not an injury itself, but a slip or trip can result in any of the aforementioned injuries | Clutter in walkways, loose extension cords, uneven pavement or floor coverings, wet or icy surfaces, and poor lighting can all be dangerous slipping and tripping hazards. | Promote a clean and organized work area, tape down extension cords, make sure walking surfaces are kept level and free from debris, water and ice, and regularly change light bulbs. |
Creating a Culture of Safety in Property Management
Chacon adds that the key to avoiding these sorts of injuries in a property management setting, where supervisors cannot always be on-site to observe and course-correct, is to develop a safety culture that permeates the organization. This includes three crucial steps:
- Be involved. Upper management must not only support but also be directly involved in the safety program themselves.“You must show some type of outward exhibition that you’re really not just talking the talk, but you’re actually walking the walk,” Chacon says.
- Go home safe. An effective safety culture doesn’t necessarily just work from top down. It also works from bottom up. So, as a property manager, you must engage workers in the injury prevention process and get them to understand and value the importance of safety.A good safety culture is one where workers police themselves and develop self-accountability for safety precautions.
“It’s an attitude of, ‘I’m going to do this because it’s the right thing and it will help me go home safely,'” Chacon says.
- Continuous improvement. A good safety culture values continuous improvement. This too stems from engaged workers who perhaps participate in safety walk-throughs or active safety committees.Workers should be encouraged to voice their safety concerns or suggestions to increase the safety of their work environments. If a dedicated safety committee does not already exist, managers should consider building one to help foster adoption and adherence of company safety policies. Click here for some tips in building an effective safety committee.
“It’s not looking for dirt,” Chacon says. “It’s not looking to see what else they can find that’s bad. It’s having a self-sufficient mindset and being willing to ask what can be done better. Then it’s having the initiative and support to implement the necessary changes.”